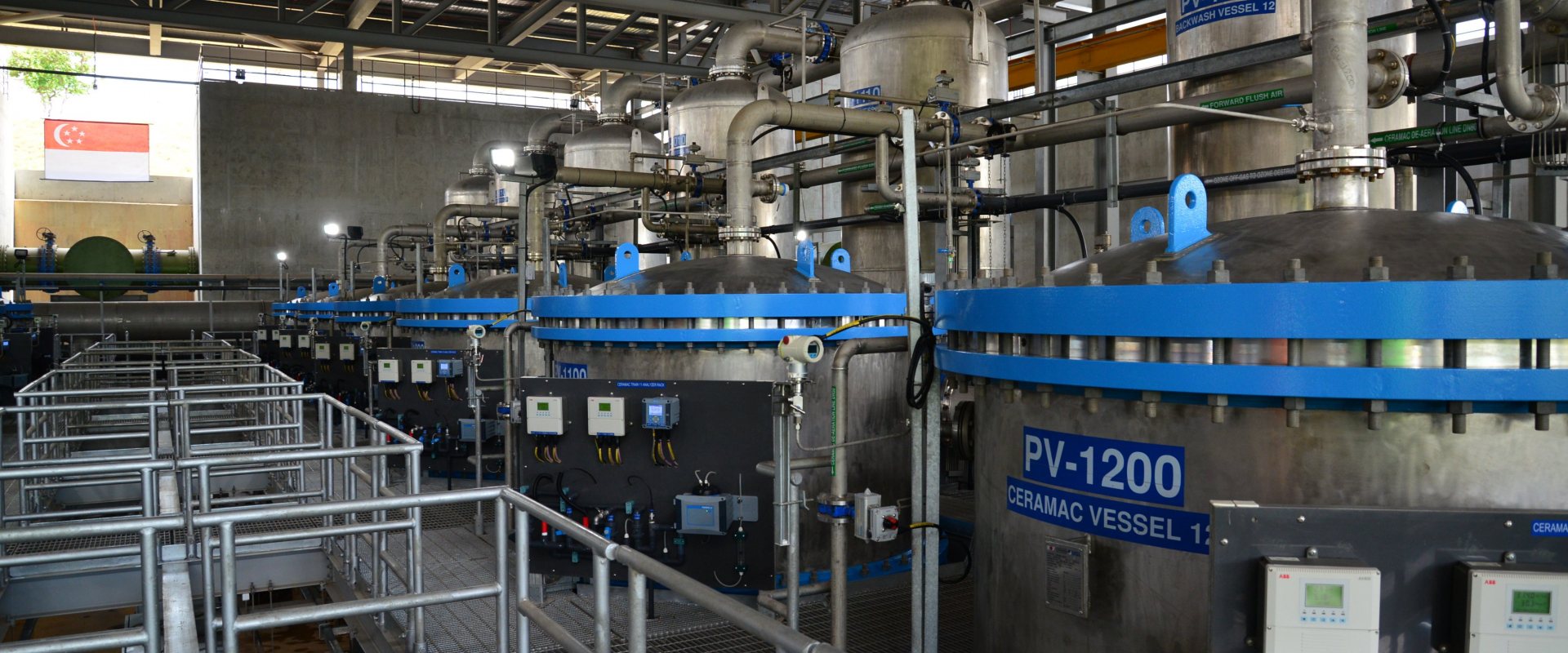
SIWW2021: Ceramic membranes gain validation as years go by
The first ceramic membranes at water treatment plants have been in use for more than twenty years and suppliers of ceramic membranes have an increasingly strong value proposition over suppliers of polymeric membranes that typically have a life span of 5-7 years.
The growing number of references, such as at the largest CeraMac plant in the world at Choa Chu Kang waterworks in Singapore, show that ceramic membranes are here to stay.
The trends in polymeric and ceramic membrane applications were discussed on several occasions during the online Singapore International Water Week 2021.
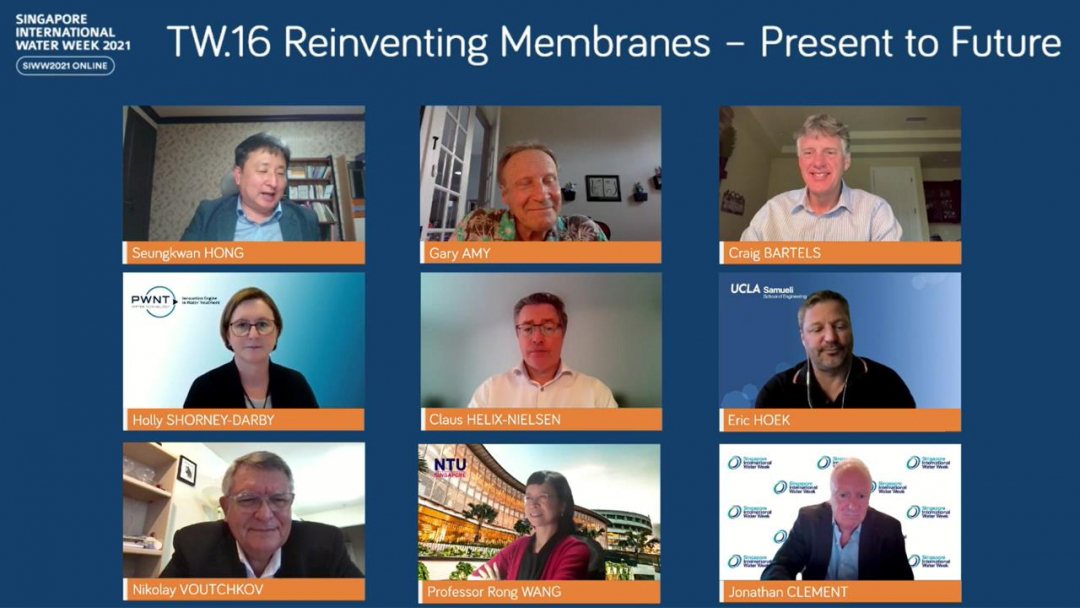
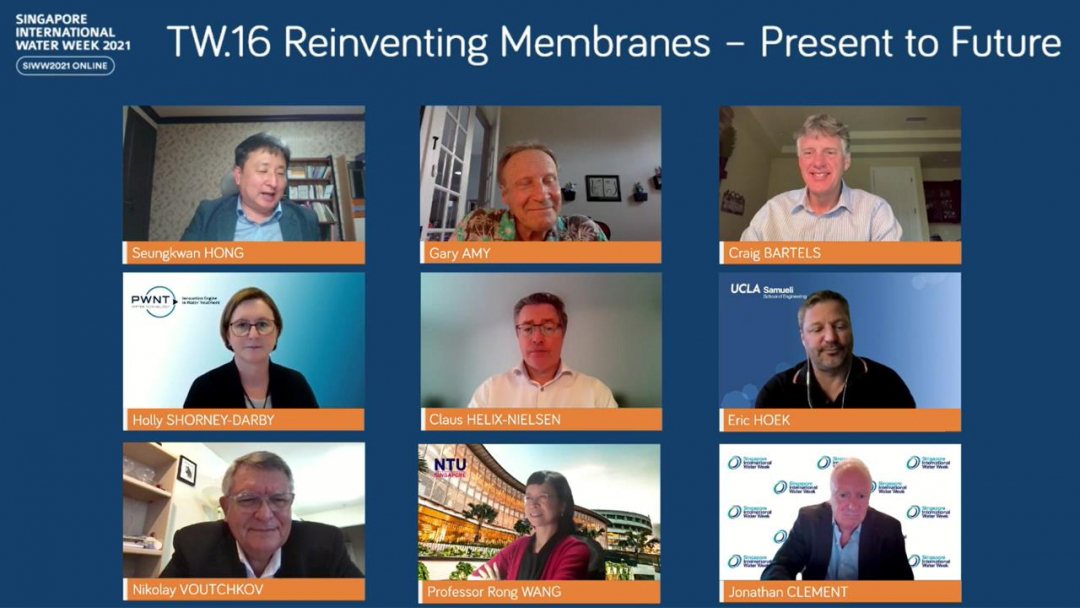
Exciting times
‘It has been exciting times”, said Holly Shorney-Darby, Head Technology Application and Piloting at PWNT, looking back on ten years of development of the CeraMac ceramic membrane water treatment system. After the first CeraMac installation for PWN in the Dutch province of North Holland|, we have completed three successful drinking water plants with our technology in the United Kingdom, Singapore and Switzerland. That has generated interest from many other water utilities around the world’, she assured.
Shorney-Darby spoke during several sessions of the SIWW2021 and noted the growing market potential for ceramic membrane filtration worldwide. 'The number of pilot plant studies is increasing. In the UK we are involved in a pilot study for recycling water and in Singapore we are developing plans to start a research study with a university.'
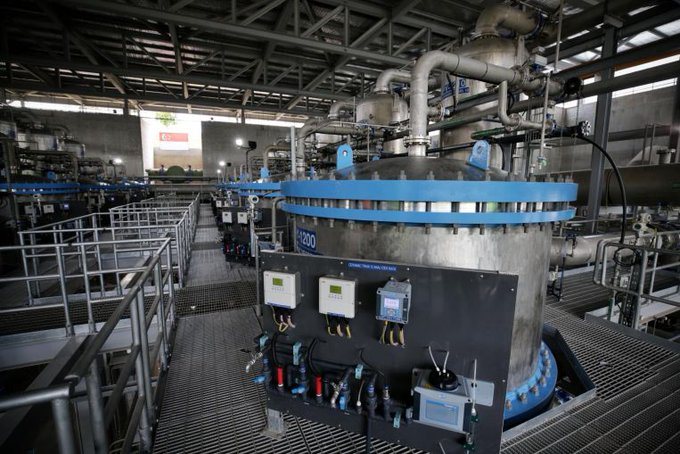
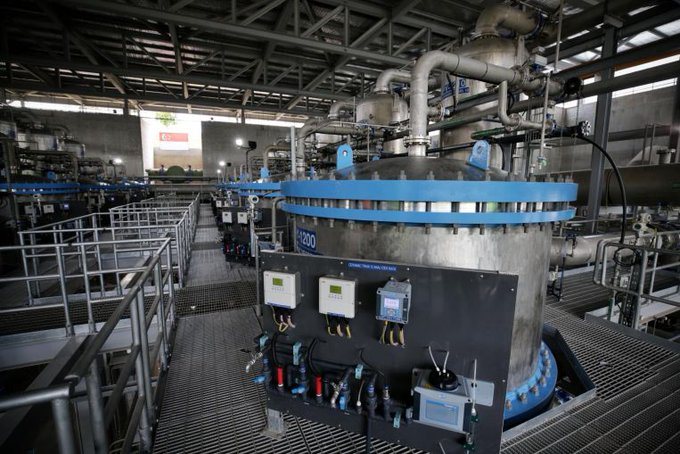
Long life span
During PWNT’s session at the SIWW2021, Stewart Sutherland, Membrane Treatment Specialist at Scottish Water described the latest development at Bonnycraig Water Treatment Works where a fourth CeraMac plant is now under construction. ‘We operate over 200 treatment plants and half of them have membrane filtration. The polymeric membranes have a relatively short life span and we wanted to learn more about the much longer life span, durability and reliability of the ceramic membranes and of CeraMac in particular.’
PWNT utilises ceramic membranes manufactured by Japanese supplier Metawater for the CeraMac system. At present, Metawater uses their membranes in single vessel systems in 160 installations worldwide; In one plant the membranes have been in operation since 1998, with no breakage events.
In addition to the ceramic material that makes the membranes more durable, the system features a unique air spring backwash technology to backwash the membranes at high pressure. The membranes are housed in a stainless steel vessel so the particles that have been removed from the water can be effectively removed from the membrane surface with high backwash pressure.
Chemicals are only used routinely to keep membranes cleaner between full cleaning events.
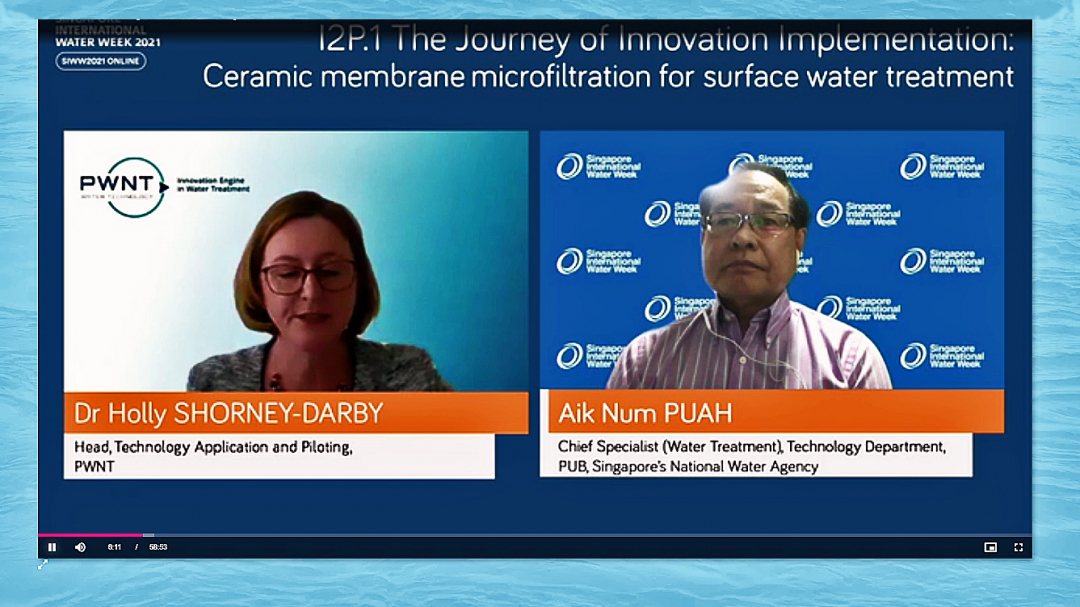
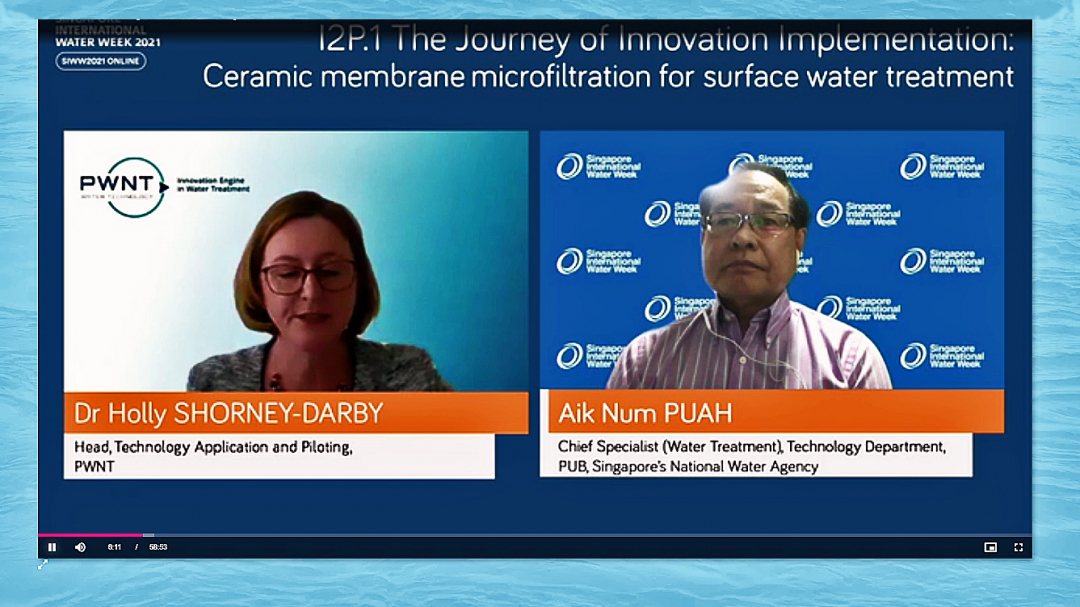
High flux
According to Sutherland, a pilot study revealed the potential of a very high flux of up to 300 liters per square meter per hour. “With our polymeric membranes we achieve in the range of 35 to 75 lmh so improvements to flux will reduce the treatment plant footprint. The air spring backwash was also proven to be remarkably efficient and effective at cleaning the membranes, even after significant fouling events.” For Scottish Water the results were promising enough to decide to build a CeraMac plant which is expected to become operational in December 2022.
PUB, Singapore’s National Water Agency, reported positive results from their Choa Chu Kang Waterworks. According to Aik Num Puah, Chief Specialist (Water Treatment) at PUB: ‘Since the CeraMac system was commissioned in May 2019, operators have continued to fine tune the system. Now, the plant is performing consistently at very stable trans membrane pressure, flux and permeability. This plant is the first to apply a continuous residual ozone on the ceramic membrane surface that has allowed the system to handle much higher organic loading that would have typically caused very bad fouling on polymeric membranes.’
Puah also shared that despite the CeraMac system having to maintain a continuous presence of residual ozone in the feed water, it was still very energy efficient. Furthermore, it was noticed that the demand for ozone on its downstream disinfection process was reduced drastically. This suggested that the combined Ceramic-Ozone had provided some disinfection while the ceramic membrane filtration was in progress.
PWNT reports low operating trans membrane pressures of less than 11 kPa on average.
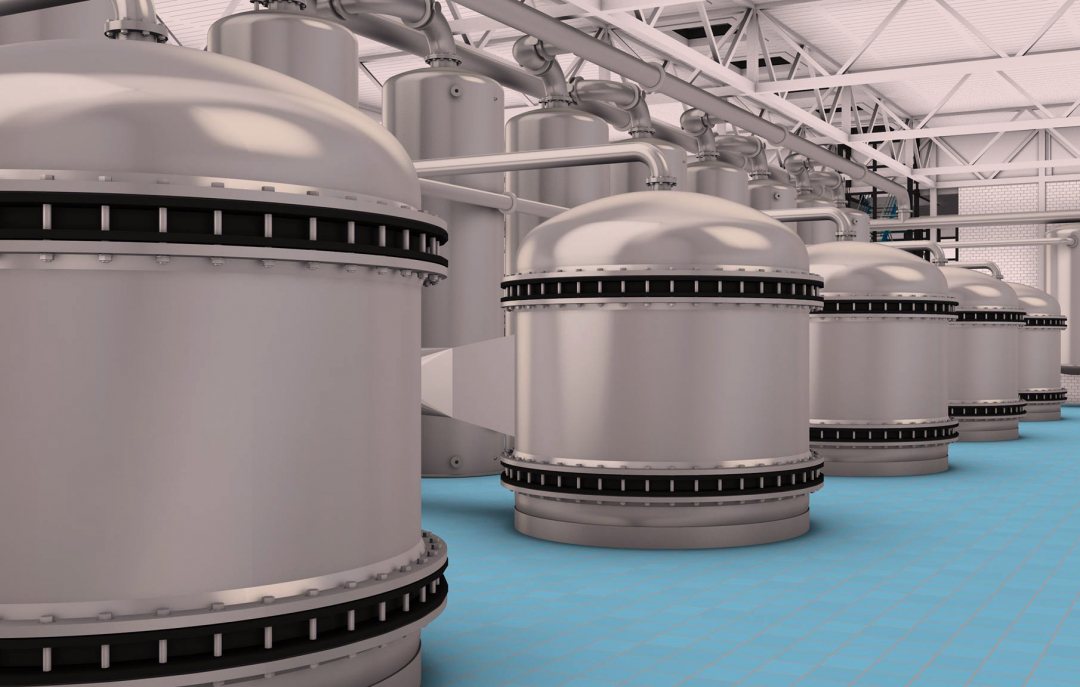
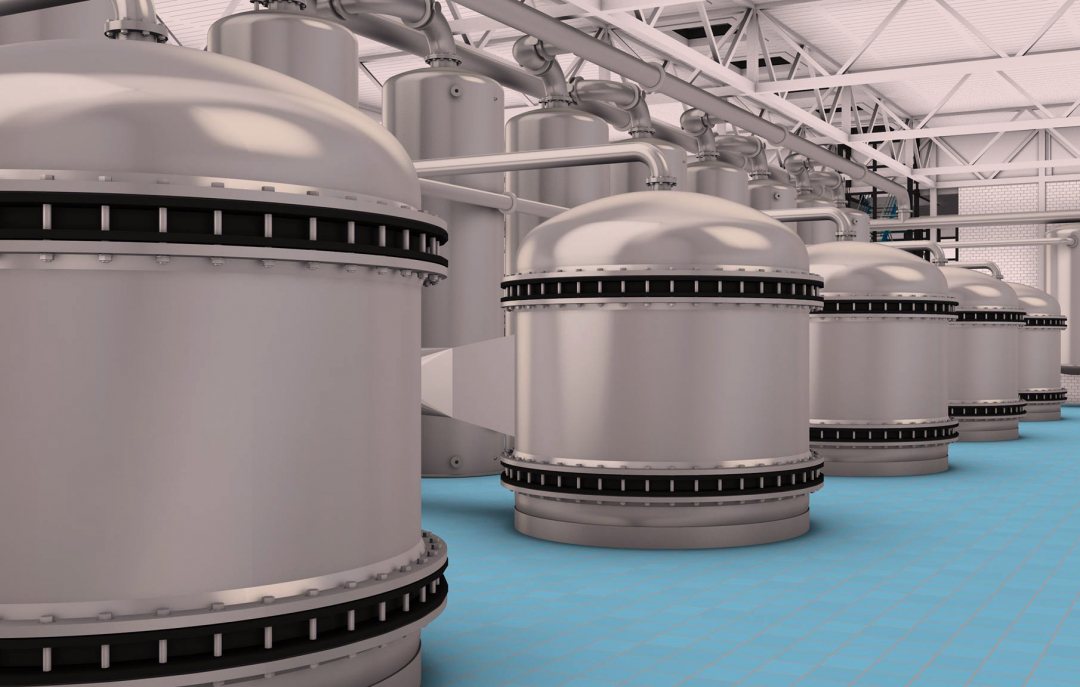
CAPEX versus OPEX
With more longer-term operational results gathered, ceramic membrane-based technologies have started to prove that the higher upfront investment costs (CAPEX) are compensated by the lower operational costs (OPEX). For PUB, evaluating the impact of both was one important reason “not to jump on the band wagon immediately”, Puah stated during the “Innovation 2 Practice” session.
According to Shorney-Darby of PWNT, operators in the drinking water sector continue to strive for robustness and lower costs. With the growing variation in sizes, configurations, ceramic materials and cleaning options, the future looks good. ‘The high fluxes and the possibility to do a heavy cleaning with more aggressive chemicals in case of a severe fouling stand out compared to polymeric membranes. But the long life durability is a key advantage’, she advocated.
The online Singapore International Water Week 2021 took place from 21 June to 2 July, presenting over 120 webinars and a virtual exhibition featuring nearly 30 companies and organisations.
More information: Singapore International Water Week 2021 and PWNT.